What is Porosity in Welding: Understanding Its Reasons and Enhancing Your Abilities
Wiki Article
Porosity in Welding: Identifying Common Issues and Implementing Best Practices for Prevention
Porosity in welding is a pervasive problem that typically goes undetected up until it triggers considerable troubles with the integrity of welds. This usual flaw can jeopardize the toughness and durability of welded frameworks, posturing safety and security threats and resulting in expensive rework. By recognizing the origin of porosity and implementing reliable avoidance methods, welders can substantially enhance the high quality and reliability of their welds. In this discussion, we will certainly discover the vital factors contributing to porosity formation, examine its detrimental results on weld efficiency, and go over the finest practices that can be adopted to decrease porosity incident in welding processes.Common Sources Of Porosity
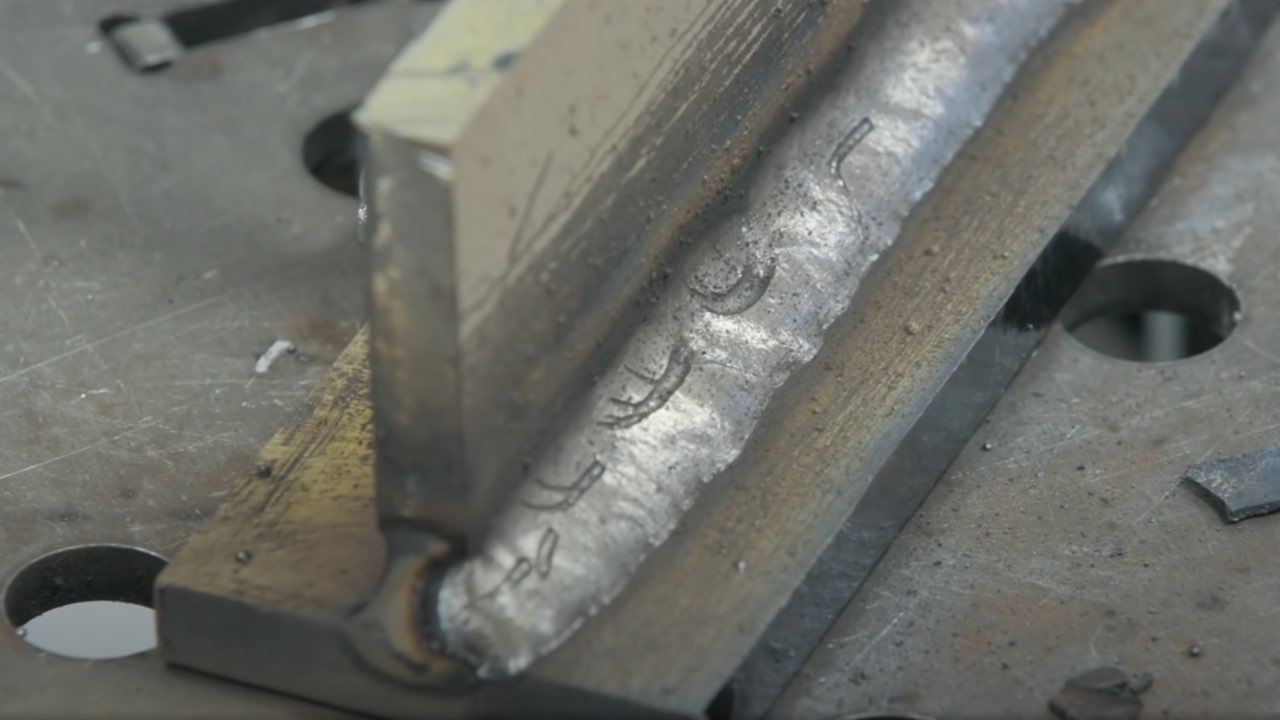
Another regular culprit behind porosity is the existence of impurities on the surface of the base steel, such as oil, oil, or rust. When these pollutants are not efficiently eliminated before welding, they can evaporate and become entraped in the weld, triggering issues. Using unclean or wet filler products can present contaminations right into the weld, adding to porosity concerns. To reduce these common reasons of porosity, comprehensive cleansing of base metals, correct securing gas option, and adherence to ideal welding specifications are essential methods in accomplishing premium, porosity-free welds.
Effect of Porosity on Weld High Quality

The visibility of porosity in welding can considerably jeopardize the structural stability and mechanical homes of welded joints. Porosity creates gaps within the weld steel, deteriorating its overall toughness and load-bearing ability. These spaces function as anxiety concentration factors, making the weld a lot more vulnerable to cracking and failure under used loads. In addition, porosity can reduce the weld's resistance to rust and various other environmental elements, further diminishing its durability and efficiency.
Among the main consequences of porosity is a decline in the weld's ductility and strength. Welds with high porosity levels tend to display reduced impact toughness and reduced capability to flaw plastically prior to fracturing. This can be specifically worrying in applications where the welded components are subjected to vibrant or cyclic loading conditions. Porosity can restrain the weld's ability to efficiently send forces, leading to premature weld failure and potential safety risks in important frameworks. What is Porosity.
Finest Practices for Porosity Avoidance
To boost the structural integrity and top quality of bonded joints, what particular measures can be applied to minimize the occurrence of porosity during the welding procedure? Porosity prevention in welding is vital to ensure the stability and strength of the final weld. One efficient technique appertains cleaning of the base metal, removing any kind of pollutants such as corrosion, oil, paint, or wetness that might result in gas entrapment. Making certain that the welding devices is in excellent condition, with clean consumables and appropriate gas flow rates, can also dramatically lower porosity. Furthermore, preserving a secure arc and regulating the welding parameters, such as voltage, present, and travel rate, aids produce a consistent weld swimming pool that minimizes the threat of gas entrapment. Using the correct welding technique for the specific product being bonded, such as readjusting the welding angle and gun position, can additionally avoid porosity. Normal examination of welds and immediate removal of any kind of issues determined during the welding procedure are vital techniques to avoid porosity and generate premium welds.Significance of Correct Welding Methods
Executing proper welding methods is critical in ensuring the architectural integrity and quality of bonded joints, building on the foundation of reliable porosity avoidance actions. Welding methods straight affect the overall stamina and resilience of the bonded structure. One vital aspect of correct welding methods is keeping the right heat input. Extreme heat can bring about enhanced porosity because of the entrapment of More about the author gases in the weld pool. Alternatively, insufficient warm may cause incomplete blend, creating prospective powerlessness in the joint. Furthermore, making use of the suitable welding criteria, such as voltage, current, and take a trip rate, is important for attaining sound welds with very little porosity.Moreover, the selection of welding procedure, whether it be MIG, TIG, or stick welding, should align with the particular demands of the job to make certain optimum outcomes. Proper cleaning and preparation of the base metal, as well as choosing the ideal filler product, are likewise necessary parts of proficient welding techniques. By adhering to these best practices, welders can minimize the risk of porosity formation and produce premium, structurally sound welds.
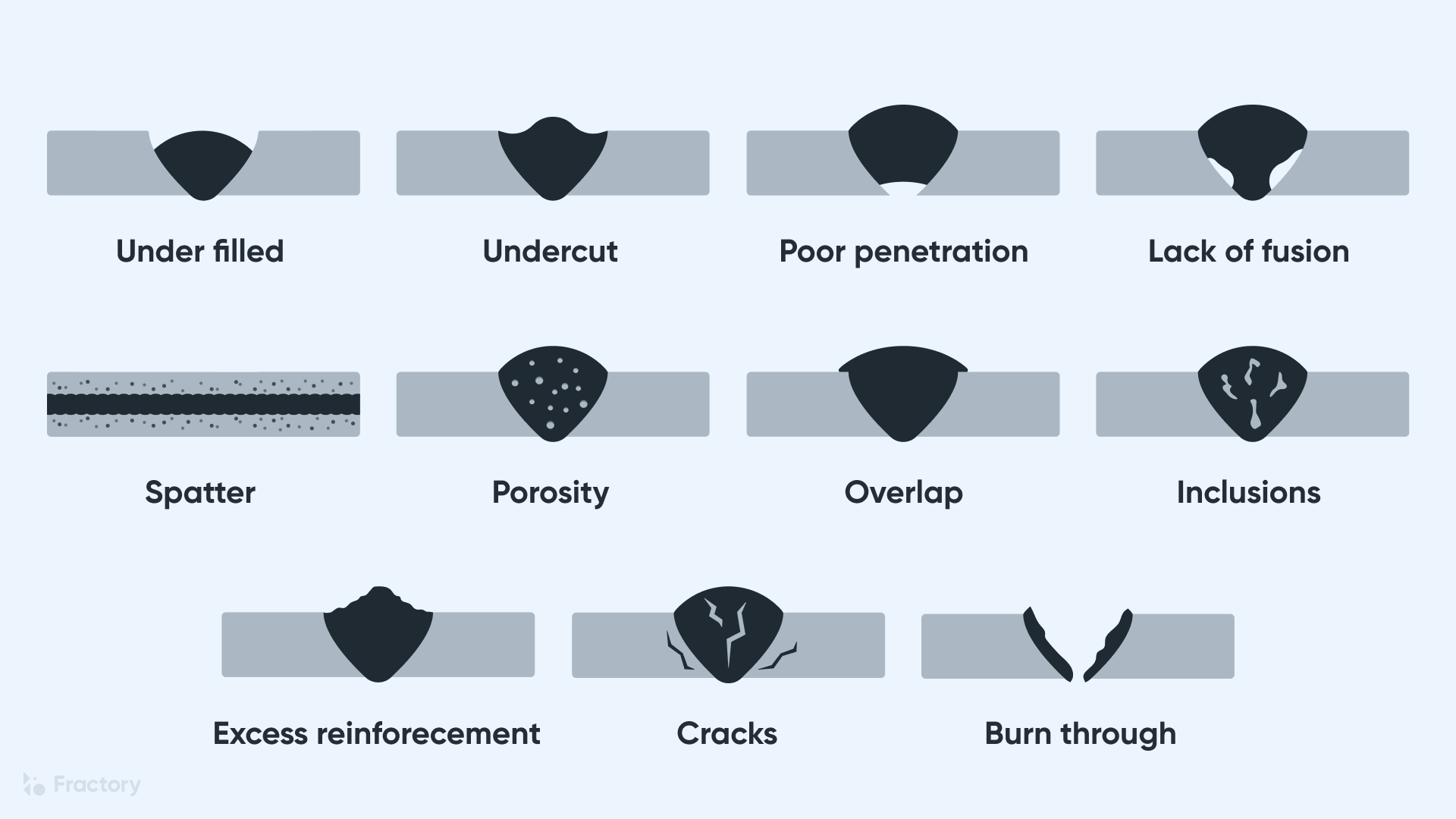
Checking and Top Quality Control Measures
Quality control steps play a critical duty in verifying the integrity and reliability of welded joints. Evaluating treatments are vital to identify and prevent porosity in welding, ensuring the strength and sturdiness of navigate to these guys the final item. Non-destructive testing techniques such as ultrasonic screening, radiographic screening, and aesthetic examination are generally used to identify potential defects like porosity. These techniques allow for the analysis of weld top quality without jeopardizing the stability of the joint. What is Porosity.Post-weld inspections, on the various other hand, assess the final weld for any type of issues, including porosity, and confirm that it fulfills defined standards. Carrying out a comprehensive high quality control strategy that consists of comprehensive screening treatments and inspections is critical to minimizing porosity concerns and ensuring the general top quality of bonded joints.
Conclusion
Finally, porosity in welding can be an usual concern that influences the top quality of welds. By recognizing the common sources of porosity and implementing best practices for prevention, this such as proper welding methods and testing procedures, welders can make sure high top quality and trusted welds. It is necessary to prioritize avoidance approaches to decrease the event of porosity and keep the honesty of bonded frameworks.Report this wiki page